CASE STUDY
Defective Boiler Circulation | Persistent Furnace Tube Failures
PLANT LOCATION | Asia |
FACILITY DESCRIPTION | Steelworks Boiler |
BOILER TYPE | Bi Drum – Natural Circulation – Firing Pulverized Coal |
BOILER CAPACITY | 600,000 [lbm/hr] |
STEAM CONDITIONS | 900 [psi] @ 900 [°F] |
Conditions:
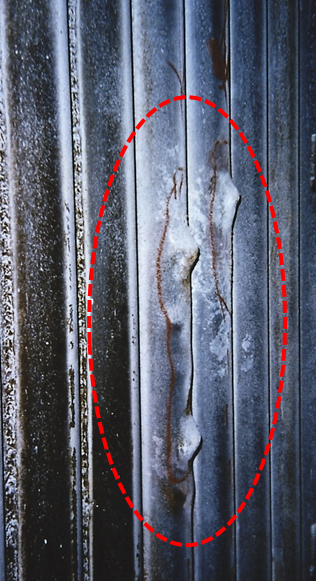
A 600,000 [lbm/hr] high pressure pulverized coal boiler operating at a steelworks experienced persistent furnace wall tube blistering within 6 months of being first commissioned. After 3 months some of the blistered tubes began to fail causing frequent forced plant outages and expensive production losses. The boiler manufacturer blamed poor water treatment, pointing to the presence of a thin scale detected on the inside surface of the tube within the zone of the failures. A new water treatment chemical supplier was engaged but despite an intense focus on optimizing water chemistry over an additional 12-month period the problem persisted.
Design Boiler was engaged to determine the cause of these failures and recommend a solution. The first step was to undertake a circulation analysis of the boiler. Design Boiler’s software was able to model its thermodynamic performance and simulate a range of operating conditions which could allow the boiler’s circulation to be evaluated.
A major defect in the boiler’s internal circulation was identified and a number of potential rectification strategies, including some which required minor reconfiguration of the boiler circulation pathways, were evaluated utilizing the computer simulation model generated previously. These simulations revealed a somewhat counter intuitive solution to the problem which involved increasing the economizer heating surface to raise the feed water temperature entering the steam drum. This effectively reduced the pre-boiling length within the heated furnace wall tubes which increased the overall circulating flow head, resulting in increased flow and improved cooling through the tubes that were previously overheating and failing.
After this change was implemented, the circulation problem was resolved and blistering tube failures no longer occurred.