CASE STUDY
HRSG | Tube Fin Burn Out
PLANT LOCATION | Asia |
FACILITY DESCRIPTION | Waste Paper Recycling Plant |
BOILER TYPE | Forced Circulation |
BOILER CAPACITY | 45 [Tonnes/hour] |
STEAM CONDITIONS | HP: 20 [Bar] @ Sat [°C] |
Conditions:
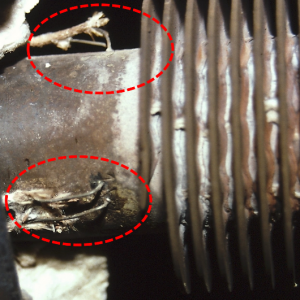
A 20 bar saturated steam Heat Recovery Steam Generator [HRSG] had recently been commissioned at a paper recycling plant. The HRSG was installed behind a 6 MW gas turbine and fitted with a duct burner to boost the boiler’s output. The HRSG was a forced circulation unit fabricated from horizontally oriented spiral wound finned tubes. It had been fitted with two circulation pumps that operated alternatively on a duty / standby basis in accordance with the applicable statutory requirements.
A little over 12 months after the boiler was commissioned the fins and tube surfaces on the first two inlet tube rows on the gas side sustained significant damage as a result of overheating. In fact the damage was so severe that some of the fin tips had begun to burn off.
Design Boiler was engaged to investigate the problem further and dispatched an engineer to site. The gas turbine was shut down briefly to allow a thorough inspection of the HRSG. This also allowed a small sample of burnt finned tubing to be removed for analysis and in addition, temporary thermocouples were installed on some of the effected tubes. As shown in the photograph, the thermocouples were fitted to the top and bottom of the un-finned surfaces of selected tubes in an attempt to detect possible flow stratification within the tubes.
Steam in boiling water flowing through heated horizontal tubes can stratify into distinct vapor and liquid layers if the water flow velocity falls below a critical limit. If stratification is occurring, the top of the tube is not cooled as effectively as the bottom of the tube and this discrepancy generates a temperature difference across the tube which can be measured.
Subsequent testing of the HRSG identified a notable temperature difference between the top and bottom of the tubes which indicated the presence of stratification. A subsequent circulation analysis of the HRSG verified that this was the likely cause of the tubes and fins becoming overheated.
Further analysis of the boiler’s circulation established that the boiler could be operated on 1 circulation pump as per its intended design provided the first 3 tube rows of the unit were replaced with un-finned plain tubes.
However, the production demands of the recycling plant meant that it was not possible to undertake this modification outside the annual shutdown period without incurring substantial production losses. The client was interested in a temporary solution that would enable the plant to continue operating until the boiler tube design/configuration could be modified during the next scheduled plant wide annual shut down.
The metallurgical analysis of the small tube sample indicated that the tube damage was limited to the outer surface of the tube body and that although the fins overheated substantially, most of the tube body had not yet been detrimentally affected by the heat damage.
In addition, further circulation analysis indicated that sufficient flow velocity to prevent further finned tube burn out could be achieved if both circulating pumps operated concurrently. This enabled the boiler to operate until the next scheduled annual shut down.
During the annual shutdown, the first three rows of tubes were replaced with plain tubes which enabled the boiler to return to service with only one circulation pump operating.
With this design modification, the boiler was able to operate reliably at its fully rated output with the duct burner in service without any tubes or fins overheating.
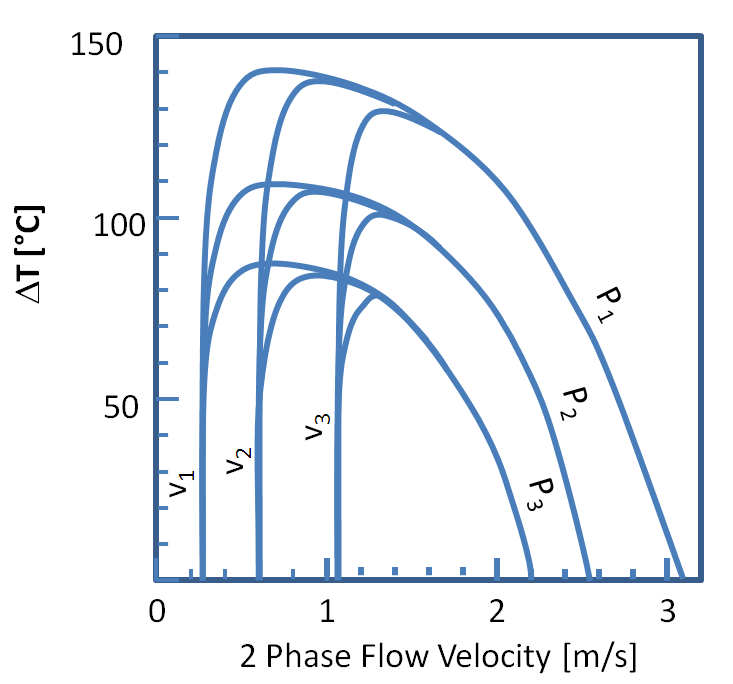