CAPABILITIES
Pulverized Coal Firing Systems
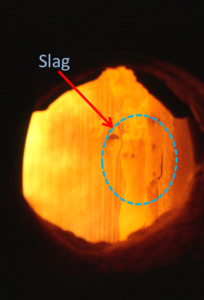
Pulverized coal [PC] firing can pose unique challenges such as poor grinding performance, high carbon in ash, slagging problems and excessively high furnace heat fluxes due to combustion related issues. There are many different pulverizing systems and each has its own specific requirements.
Design Boiler has extensive experience in troubleshooting problems associated with pulverized coal firing systems on both utility and industrial boilers, firing a wide range of coals including high moisture lignite and high ash bituminous coal. Design boiler is also skilled and experienced in optimizing the performance of pulverizer operating plant including ball mills, beater mills and roller mill pulverizers.
Our capabilities in this field are summarized below.
- Pulverizer Set up This normally includes the adjustment of classifier settings, balancing the fuel flow through the PC pipes, setting the mill outlet temperature control limits and calibrating the primary air flow measuring device. Different coal types require different settings.
- Troubleshooting and optimization. These capabilities extend to a wide range of pulverizers including ball mills , grinding mills and beater mills.
- Measurement of PC fines distribution This is an effective means of monitoring the condition of a mill and scheduling mill maintenance.
Typical Pulverized Coal Investigation Scenario: A pulverized coal fired boiler experiences furnace slagging and elevated carbon in ash after changing coal suppliers. An investigation to remedy this problem may involve the following activities:
Site Visit & Testing:
- A series of pulverized coal [PC] sampling tests are conducted on each pulverizer in accordance with recognized procedures (typically ASTM PTC 4.2). This sometimes requires installation of dustless connectors and measurement of primary airflow through PC pipes.
- The particle size distribution of the PC samples is determined by laboratory sieve analysis.
- The critical pulverized coal [PC] fineness is defined as the optimum mass proportion of PC that passes through a set grade of mesh. High values of this proportion point to the pulverizer over grinding, consuming excessive power and requiring more frequent maintenance. Low values of this proportion will detrimentally effect combustion and potentially raise the carbon in ash. Critical values of PC fineness varies with coal type and firing system used.
Analysis of Results:
- The mill outlet temperature of each pulverizer is assessed against best practice criteria. The mill outlet temperature is a direct function of fuel moisture, the mill fuel air ratio and the primary air inlet temperature. If not correctly set it can adversely effect mill performance and burner combustion. It can also contribute to slagging problems in some coal species. Multiple mills grinding the same coal should be maintaining approximately the same mill outlet temperature.
Implementation and remedial actions:
- Excessively fine coal is addressed by adjusting the pulverizer classifier settings. Options for addressing low mill fineness include:
- readjusting the pulverizer classifier settings; and/or
- completely overhauling the pulverizer which Design Boiler is able to supervise and manage.
- Significant pulverized fuel distribution anomalies across the fuel pipes exiting the pulverizer may need to be re-balanced by installing flow resisting orifices in some of the fuel pipes. Design Boiler can supply bespoke designed flow restrictors for this purpose.
- Inspection of the internal coal feeder belt and re-calibration of its weighing cells is often required.
- Strategies are implemented to facilitate improved monitoring of pulverizer performance. This may include assistance with scheduling pulverizer maintenance.